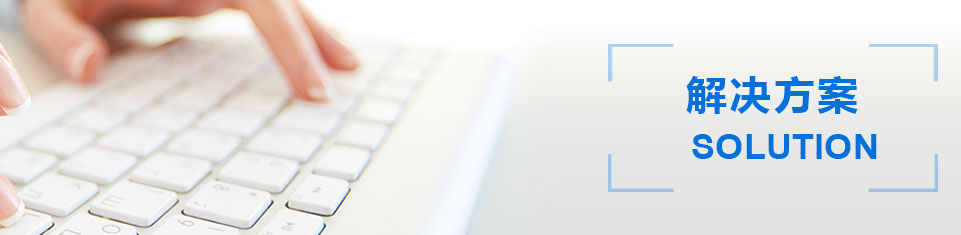
工业铝型材化学抛光中问题分析与对策
①铝锭中铝的纯度不够,采用铝纯度大于99.7%的铝锭来进行化学抛光可获得光亮的表面。
②电解槽中硝酸的含量要控制得当,含量过低,使型材表面铜的附着量增多,造成光亮度不够;含量过高,使铝型材表面模糊或形成彩虹膜,也会造成光亮度不够,所以要根据抛光量的多少而调整硝酸的浓度。
③抛光时间太短,适当调整化学抛光的时间。
④温度不够,将槽液的温度调整至好的状态。
⑤搅拌不匀,充分搅拌槽液中的铝型材使其与抛光均匀。
⑥槽液老化,根据使用情况要不定时更换槽液,确保槽液的化学成份合格。
⑦槽液的相对密度大,密度过大的槽液会使铝型材浮出液面,导致浮出的部分抛光不匀。
⑧铝型材带水份,将带有水份的铝型材放入槽内抛光,降低了槽液的浓度,也会造成抛光不够光亮,应该注意使用干燥的铝型材,以免影响抛光效果。

二:白色沉淀物附着
经化学抛光后的铝型材表面附着一层分布不均匀的白色沉淀物,是由于电解槽中溶铝量太高,将槽液的相对密度控制在1.80以上,并将槽液中的溶铝量调整至正常范围。
三:表面粗糙
①槽液中硝酸的含量过高,调整硝酸的含量,以免酸性浸蚀而使化学抛光反应过于剧烈而造成铝型材表面粗糙。
②硝酸含量正常,铜的含量过高,则要根据槽液中铜的来源,如果是添加剂铜含量高,则要少加入,如果是含铜量高的铝型材,则要采用不含铜的添加剂来进行化学抛光,使槽液中铜的含量保持在正常范围之内。
③铝材内部晶粒细化不充分,疏松和夹渣等缺陷,需提高铝材的质量。
四:转移性浸蚀
化学抛光后的铝型材表面带有浅蓝色,可能是槽液中硫酸含量过高引起的,因为铝型材从高温的槽液中提取出来时,表面仍在剧烈反应使硝酸快速消耗,要尽快转移到水洗槽中,并进行充分搅拌水洗。
五:点腐蚀
①硝酸含量偏低,及时补充硝酸使之含量到规定的范围之内。
②铝型材表面气体累积形成气孔,应使工件的倾斜度加大,快速搅拌使气体挥发出来。
③铝型材表面有残留的烤干后的印痕,则应该加强铝型材表面的化学水洗,提高表面质量。