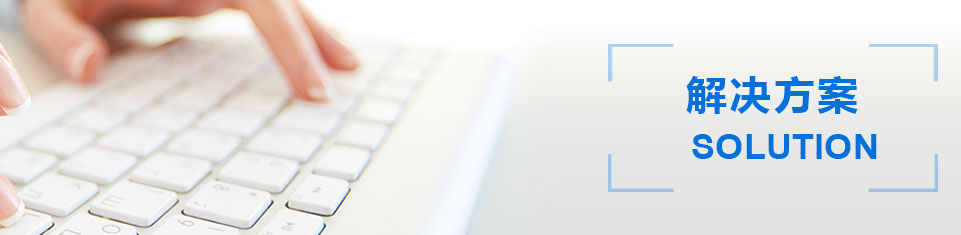
为什么说快速换线是精益管生产的基本特征
精益管生产线多品种、小批量就意味着生产一种产品没有多少量,就要马上去生产另外一个产品,如此类推。这样的更换在一天里面可能会非常频繁,所以生产线需要频繁的换线,以设备为主的流程则需要频繁地换模具,这种换线换模因为发生频繁,总计将带来很多时间上的浪费。如果不加以改进,生产将处于混乱当中,每天真正有价值的时间将剩无几。
所以精益管生产必需要进行一项工作,就是缩短换线换模的时间。丰田公司将这种快速换线换模的方式称为SMED,即Single Minute Exchange of Die,翻译为单分钟,即10分钟内更换模具。
所以SMED实质上就指在尽可能的短时间里,完成不同产品需要理换模具的过程。SMED所提到的减少换模时间的目标就是10分钟。
实施SMED的直接目的就是降低换模换线时间。它也带来了很多好处:
(1)、使得作业更轻松、简单、安全。SMED改善后,换模过程标准化了,治具标准化了,作业自然更加轻松、简单。
(2)、提高设备利用率及设备稼动率。换线换模这种无效工时减少了,设备的利用率及稼动率在其他不变的情况下自然也得以提升。
(3)、减少了批量大小。如果换线换模非常短,生产排配奖变得非常轻松,几乎完全可以跟随客户的变化,随时安排生产的转换。这样生产的批量也可以尽可能的小。
如下图就是一个简单图示说明,假设目前换模时间为2h,生产实践为18h,生产批量为10K。
(4)、降低库存水平。紧随客户需求,随时调整批量大小,产品做出来立即可以转送到客户手中,成品的库存自然降低不少。另外,因为批量小,所以那种为了等整批生产完,前面做完的产品不得不等待的现象也得以消除。
(5)、提高生产效率。缩短了无效时间,提升了时间利用率,生产的效率可以得到相应的大幅提高。
(6)、减少浪费。这之中可以看到,减少了等待、调试时制造不良品、制造过多、库存等多方面的浪费,将会给生产带来巨大的经济效益。
(7)、缩短交货期。客户随时要,我们可以随时更换,而不是如传统大批量生产方式那样,必须等前一批产品生产完才能更换,自然交换期就会缩短。